- Jayesh Dyes & Chemicals
This shade card illustrates our range of JAYVAT Vat printing pastes, that are suitable for roller, screen printing on cellulosic fibers, viz. mercerized and unmerserized cotton, spun and filament viscose.-
- Introduction (contd.)...The Pastes fix rapidly when applied by the potash/Rangolite process and are less sensitive to variations in the concentration of these reagents than are ordinary vat dyestuff. Since the particle size is extremely small, they are less effected by adverse steaming conditions than ordinary brands. They are suitable for direct style printing, as well as illuminants on a dischargeable grounds like reactives, naptols, directs etc. They are supplied in a non-setting, non dying from and have relative high degree of storage stability.
-
- Tech SpecificationsJAYVATFastness toLight
1/1Washing ISO4ChlorineJayvat Yellow GCN (MD) Paste4-555Jayvat Golden Yellow GOK (MD) Paste5-645Jayvat Orange RF (MD) Paste545-4Jayvat Scarlet GGN (MD) Paste5-64-54-5Jayvat Pink R (MD) Paste64-55Jayvat Violet RRN (MD) Paste64-55Jayvat Violet 2R (MD) Paste6-755Jayvat Blue 4B (MD) Paste4-553-4Jayvat Indigo Blue 4G (MD) Paste43-43-4Jayvat Jade Green FFB (MD) Paste755Jayvat jade Green 2G (MD) Paste6-74-54Jayvat Brown RRD (MD) Paste74-54-5Jayvat Grey 3B (MD) Paste5-665Jayvat Black BG (MD) Paste6-754 -
- Preparation of Printing PasteThe choice of thickening depends on the dyestuff used, steaming condition, type of fabric to be printed, and washing off facilities available. The thickners commonly used are mixture of starches, gum tragacanth Indalca AGBV, British gum (Dextrine) etc. Additional of British gum, because of its pronounced reducing action. Ensure uniform level prints, even under unsuitable ageing condition.
-
- Stock Thickening
Stock Thickening
110 gmsMaize starch is mixed well with180 gmsWater110 gmsGum tragacanth (6%)250 gmsBritish gum (Dextrine)
Mixture cooked, with constant stirring, till homogenous transparent mass Obtained.
After cooling to 80o C, add150 gmsPotassium carbonate. Cool to 50* C and add50 gmsGlycerine150 gmsRangolite CPrint Paste Recipe
25-100gms JAYVAT paste150-250gms water625-750gms stock paste -
- Reduction ThickeningThis is to obtain lower depth of shades from the standard print pastes. It is kept ready for conversion of standard print pastes into different strengths. Reduction thickening pastes is prepared in a similar manner as stock paste but using lower quantities of alkali (5%) and Rangolite (10%)
-
- Processing After Printing
Drying:
The printed material has to be thoroughly dried at moderate temperature (not exceeding 50-60o C). Care should be taken that the atmosphere in which prints are dried is not damp and that goods are not over dried, since reducing agent may decompose partially and thus becomes ineffective when prints are subsequently fixed by ageing. The prints should not be exposed to sunlight either before, during, or after drying. After drying, the goods should be cooled and steamed with the least possible delay, i.e. within a few hours, where this is impracticable the goods should be stored in a dry atmosphere, free from moisture (steam) and acid fumes.Steaming:
Vat prints are to be steamed under the most suitable condition if best results are to be obtained. The prints have to be steamed for 10-15 minutes in rapid ager by air free, highly saturated steam at 101-103o C. Where only starager is available, batchwise steaming at 100-102o C is done for 20-30 minutes. Water content, temperature and volume of steam must be kept as constant as possible to ensure uniform prints. After steaming goods are cooled and kept in a cool dry place until they are washed off.Oxidation:
The steamed vat prints are given a short rinse in cold running water and oxidized at 40o to 50o C with 2 gms / litre sodium per borate or hydrogen peroxide, or sodium dichromate and 1 gms / litre Glacial Acetic Acid.Soaping:
After Oxidation, wash and treat at boil with 2-3 gms / litre Lissapol D Paste and 2 gms / litre soda ash. For viscose fabrics. Soaping is done at 80oC without additional of soda ash. -
- NotesFixation of colour is improved if print pastes are kept overnight before use. For JAYVAT Black BG, further additional or potash and Rangolite required. Potash may be replaced by Sodium carbonates is some cases. However since soda is not hygroscopic, less intense shades would be obtained, if ageing is carried out in slightly superheated steam. Addition to 30 gms / kg of dispersing agent prevents thickening of the print paste. Especially recommended for Orange RF and Scarlet GGN. The print paste may be filtered through a fine cloth before printing, to remove hard particles, present if any, from various ingredients. In certain indigoid type of dyes, better results, may be obtained by addition of 30 gms / kg solution salt B. It is advantageous to add 30 gms / kg formaldehyde (40%) to increase stability of print paste towards humidity. Without guarantee
Jayesh Dyes & Chemicals
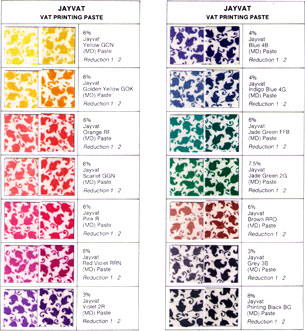
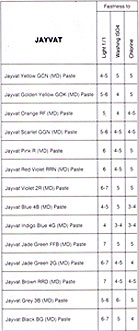
Inroduction
This shade card illustrates our range of JAYVAT Vat printing pastes, that are suitable for roller, screen printing on cellulosic fibers, viz. mercerized and unmerserized cotton, spun and filament viscose. They fix rapidly when applied by the potash/Rangolite process and are less sensitive to variations in the concentration of these reagents than are ordinary vat dyestuff. Since the particle size is extremely small, they are less effected by adverse steaming conditions than ordinary brands. They are suitable for direct style printing, as well as illuminants on a dischargeable grounds like reactives, naptols, directs etc. They are supplied in a non-setting, non dying from and have relative high degree of storage stability.Preparation of Printing Paste
The choice of thickening depends on the dyestuff used, steaming condition, type of fabric to be printed, and washing off facilities available. The thickners commonly used are mixture of starches, gum tragacanth Indalca AGBV, British gum (Dextrine) etc. Additional of British gum, because of its pronounced reducing action. Ensure uniform level prints, even under unsuitable ageing condition.Stock Thickening
110 gms
Maize starch is mixed well with
180 gms
Water
110 gms
Gum tragacanth (6%)
250 gms
British gum (Dextrine)
Mixture cooked, with constant stirring, till homogenous transparent mass Obtained.
After cooling to 80o C, add
Mixture cooked, with constant stirring, till homogenous transparent mass Obtained.
After cooling to 80o C, add
150 gms
Potassium carbonate. Cool to 50* C and add
50 gms
Glycerine
150 gms
Rangolite C
Print Paste Recipe
25-100
gms JAYVAT paste
150-250
gms water
625-750
gms stock paste
Reduction Thickening
This is to obtain lower depth of shades from the standard print pastes. It is kept ready for conversion of standard print pastes into different strengths. Reduction thickening pastes is prepared in a similar manner as stock paste but using lower quantities of alkali (5%) and Rangolite (10%)Processing After Printing
Drying:
The printed material has to be thoroughly dried at moderate temperature (not exceeding 50-60o C). Care should be taken that the atmosphere in which prints are dried is not damp and that goods are not over dried, since reducing agent may decompose partially and thus becomes ineffective when prints are subsequently fixed by ageing. The prints should not be exposed to sunlight either before, during, or after drying. After drying, the goods should be cooled and steamed with the least possible delay, i.e. within a few hours, where this is impracticable the goods should be stored in a dry atmosphere, free from moisture (steam) and acid fumes.Steaming:
Vat prints are to be steamed under the most suitable condition if best results are to be obtained. The prints have to be steamed for 10-15 minutes in rapid ager by air free, highly saturated steam at 101-103o C. Where only starager is available, batchwise steaming at 100-102o C is done for 20-30 minutes. Water content, temperature and volume of steam must be kept as constant as possible to ensure uniform prints. After steaming goods are cooled and kept in a cool dry place until they are washed off.Oxidation:
The steamed vat prints are given a short rinse in cold running water and oxidized at 40o to 50o C with 2 gms / litre sodium per borate or hydrogen peroxide, or sodium dichromate and 1 gms / litre Glacial Acetic Acid.Soaping:
After Oxidation, wash and treat at boil with 2-3 gms / litre Lissapol D Paste and 2 gms / litre soda ash. For viscose fabrics. Soaping is done at 80oC without additional of soda ash.Notes:
Fixation of colour is improved if print pastes are kept overnight before use. For JAYVAT Black BG, further additional or potash and Rangolite required. Potash may be replaced by Sodium carbonates is some cases. However since soda is not hygroscopic, less intense shades would be obtained, if ageing is carried out in slightly superheated steam. Addition to 30 gms / kg of dispersing agent prevents thickening of the print paste. Especially recommended for Orange RF and Scarlet GGN. The print paste may be filtered through a fine cloth before printing, to remove hard particles, present if any, from various ingredients. In certain indigoid type of dyes, better results, may be obtained by addition of 30 gms / kg solution salt B. It is advantageous to add 30 gms / kg formaldehyde (40%) to increase stability of print paste towards humidity. Without guarantee